VERTICAL CONTINUOUS VACUUM PAN (VKT)
BMA’s vertical continuous vacuum pan “VKT” (Verdampfungs-Kristallisations-Turm) is based on a proved design principle: the vertical cylindrical crystallization chamber of the batch pan. It allows the use of mechanical circulators ensuring excellent circulation and mixing of the massecuite.
The VKT consists of superimposed crystallization chambers, i.e. it is a cascade of stirring vessels, where the massecuite flows from top to bottom under its own gravity. The forced circulation practised, in conjunction with constantly low massecuite levels, allows the use of low-pressure heating steam, as the hydrostatic pressure of the massecuite column in a continuously operating unit is much lower than in a conventional pan.
Each VKT chamber can be adjusted separately, a fact which ensures safe and continuous operation and brings about technological advantages such as:
- Uniform tapping of heating steam from evaporators,
- Uniform tapping of feed solution.
- Uniform vapour tapping and condenser loading
- Uniform massecuite discharge.
Due to the residence time behaviour in continuous crystallization, the crystal size distribution is slightly wider in the coarse crystal range. In actual practice the coefficients of variation are therefore somewhat inferior to those achieved in batch operation. However, the decisive criterion influencing the quality of the product is the quality and quantity of seed added in relation to the product.
VKT cleaning:
A fundamental demand made on a continuously operating vacuum pan is that it is available throughout the campaign without any total plant standstills. It is a well-known fact that incrustations cannot be fully avoided – especially where high-purity massecuites are involved.
A requirement for all VKTs is that it must work without interruptions during the whole harvest. This is the cause of a problem, since it is not possible to avoid scale, especially in the case of masses with high purity, so in general it is necessary to empty the tank for cleaning.
The vertical cascaded design of the VKT meets this requirement ideally. The fact that a chamber can be bypassed, allows it to be disconnected from the process, while the other ones continue to operate.
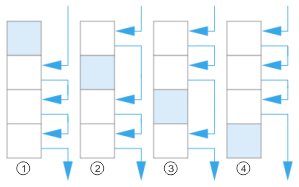
Schematic view of the cleaning process for VKT BMA
For the cleaning of the crystallisation chambers, the control system changes the operating conditions, so, for example, when it is necessary to clean the chamber 1 the massed mass is directed to the chamber 2; when camera 2 is cleaned, the level signal from camera 1 is directed to the mass feed valve of the by-pass line, transferring the mass from camera 1 to camera 3; when camera 4 is cleaned, the level signal from chamber 3 is directed to the mass discharge pump to control the exit velocity.
The massecuite drain and the cleaning solution are carried out by different pipes. All the sensors are equipped with steam cleaning systems to avoid incrustations and ensure their correct operation throughout the harvest.
BMA VKT Characteristics and advantages:
- Excellent mass circulation is achieved with the combination of mechanical agitators and chambers designed for optimum flow. The efficient forced circulation by the agitators and a low level of mass on the calenders substantially improves the heat transfer. The VKT system offers great advantages in the aspect of energy saving, since the principle of evapo-crystallization operates at low levels of temperature and allows the use of heating steam at low pressure; this allows the evaporation plant to work at a lower temperature level.
- The fact that the VKT is heated by steam coming from the last evaporator effect (up to a sixth effect) allows to increase the evaporation in the whole plant and, as a result of this, to produce masses with a high level of dry substance with a remarkable energy saving.
- Uniform flows of steam and feed solution, as well as uniform discharges of cooked massecuite, vapored and condensed, result in an extremely uniform and smooth operation of the tank, reflected in the operation of the entire plant and in particular in the area of evaporators .
- The arrangement of the crystallization chambers avoids the remixing of the mass. This helps to obtain a more uniform crystal size, significantly improving the performance of the spin, reducing returns, saving energy and increasing the overall performance of the mill.
- The mechanical agitators of the VKT system allow to work with feeding solutions with a higher content of dry matter than the one admitted in horizontal crystallisation systems. Likewise, the final content of dry substance in the final massecuite is considerably higher than that reached in horizontal systems.
- No additional cup holders are required for the cleaning cycle. The operating cycle of a VKT for white sugar or raw sugar is approximately 3 to 4 weeks. The VKT for C has to be cleaned only once per harvest; even, under optimal conditions, it may not need to be cleaned throughout the harvest.
- Even if it is necessary to retain the massecuite (due to some fault in some part of the process, for example), the agitators will keep the adequate conditions in the chambers for periods of up to several days. The VKT will not need to be emptied at these stops.
- To complete the operation of the VKT, all the feed solution it contains will be converted into a final massecuite, which eliminates the need for an additional massecuite container; this represents a great advantage compared to horizontal continuous pans.
- The VKT has several implements to eliminate incrustations. It is for this reason that the periods between cleanings are so long. It has devices to moisten the internal walls of the steam chambers and the massecuite pipelines. The solution applied to the walls prevents the massecuite adherence to them and prevents issues in the steam chambers and valves during operation. Each crystallisation chamber can be disconnected from the process and bypassed for cleaning purposes. When automatically increase the load to another chambers, a constant flow is ensured even during these cleaning stages.
- It is possible to increase the capacity of the VKT simply by adding a more crystallisation chamber. It is also possible to install it both inside and outside. It does not require expensive structures or the construction of special buildings. A simple concrete foundation is enough. The vertical tower design means short installation times.
Image Gallery: